Aujourd'hui, ce principe s'est largement répandu à travers le monde industriel.
Les besoins et les resourcesDans la méthode MRP, on répartit les "besoins" en deux catégories :
- Les besoins indépendants appelés également besoins aléatoires ou externes
- Les besoins dépendants, appelés également besoins induits ou internes
Les besoins externes sont les commandes du client fermes ou prévisionnelles ou des estimations de vente. Les besoins internes sont les besoins en composants (sous-ensembles fabriqués ou composants achetés), provoqués par la déclaration d'un OF sur un article du niveau supérieur.
Les ressources sont les entrées en stock, fermes ou prévisionnelles qui vont permettre de combler un besoin. Les ressources sont :
- Les réceptions d'ordres de fabrication
- Les réceptions de matière première et de composants achetés
Avec la méthode MRP
- les seuls besoins faisant l'objet d'une estimation probabiliste sont les besoins externes
- les besoins induits sont calculés, c'est la notion à retenir en priorité
- du stock actuel
- des ressources (fabrication en cours, approvsionnement en cours)
- du stock minimum de sécurité
- des quantités de lancement pour les produits fabriqués et des quantités convenues avec le fournisseur pour les produits achetés
Le nombre de boucles est inférieur ou égal au Low Level Code
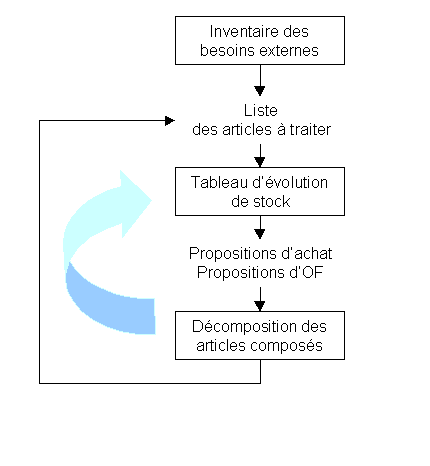
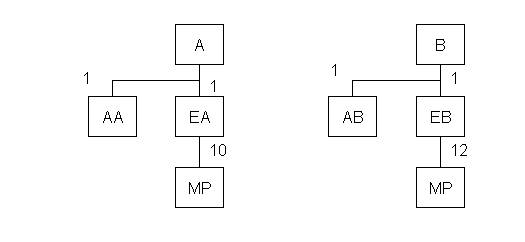
A cause d'une nouvelle technologie utilisée pour les produits B, les délais de fabrication et la qualité obtenue sont plus aléatoires que pour le produit A.On décide donc de constituer un stock tampon de produits finis B de 50 unités.
Dans cette entreprise, le low level code est donc égal à 3.
Article | Délai d'appro. / Fab. | Quantité de lancement | Minimum de sécurité | Stock à la semaine S |
---|---|---|---|---|
A | 5 semaines | 100 | 0 | 47 |
B | 3 semaines | 100 | 50 | 53 |
EA | 1 semaine | 30 | 0 | 10 |
EB | 1 semaine | 30 | 0 | 0 |
AA | 4 semaines | 200 | 0 | 12 |
AB | 4 semaines | 200 | 0 | 125 |
MP | 8 semaines | 3000 | 0 | 256 |
Date | S+2 | S+5 | S+18 | S+20 |
---|---|---|---|---|
Quantité | 20 | 60 | 120 | 100 |
Date prévue | Stock avant | Besoin | Ressource | Stock après | Proposition |
---|---|---|---|---|---|
S | 47 | 0 | 0 | 47 | 0 |
S+1 | 47 | 0 | 0 | 47 | 0 |
S+2 | 47 | 20 | 0 | 27 | 0 |
S+3 | 27 | 0 | 0 | 27 | 0 |
S+4 | 27 | 0 | 0 | 27 | 0 |
S+5 | 27 | 60 | 0 | -33 | 100 |
S+6 | 67 | 0 | 0 | 67 | 0 |
S+7 | 67 | 0 | 0 | 67 | 0 |
S+8 | 67 | 0 | 0 | 67 | 0 |
S+9 | 67 | 0 | 0 | 67 | 0 |
S+10 | 67 | 0 | 0 | 67 | 0 |
S+11 | 67 | 0 | 0 | 67 | 0 |
S+12 | 67 | 0 | 0 | 67 | 0 |
S+13 | 67 | 0 | 0 | 67 | 0 |
S+14 | 67 | 0 | 0 | 67 | 0 |
S+15 | 67 | 0 | 0 | 67 | 0 |
S+16 | 67 | 0 | 0 | 67 | 0 |
S+17 | 67 | 0 | 0 | 67 | 0 |
S+18 | 67 | 120 | 0 | -53 | 100 |
S+19 | 47 | 0 | 0 | 47 | 0 |
S+20 | 47 | 100 | 0 | -53 | 100 |
S+21 | 47 | 0 | 0 | 47 | 0 |
Date prévue | Stock avant | Besoin | Ressource | Stock après | Proposition |
---|---|---|---|---|---|
S | 10 | 100 | 120 | 30 | 0 |
S+1 | 30 | 0 | 0 | 30 | 0 |
S+2 | 30 | 0 | 0 | 30 | 0 |
S+3 | 30 | 0 | 0 | 30 | 0 |
S+4 | 30 | 0 | 0 | 30 | 0 |
S+5 | 30 | 0 | 0 | 30 | 0 |
S+6 | 30 | 0 | 0 | 30 | 0 |
S+7 | 30 | 0 | 0 | 30 | 0 |
S+8 | 30 | 0 | 0 | 30 | 0 |
S+9 | 30 | 0 | 0 | 30 | 0 |
S+10 | 30 | 0 | 0 | 30 | 0 |
S+11 | 30 | 0 | 0 | 30 | 0 |
S+12 | 30 | 0 | 0 | 30 | 0 |
S+13 | 30 | 100 | 0 | -70 | 90 |
S+14 | 20 | 0 | 0 | 20 | 0 |
S+15 | 20 | 100 | 0 | -80 | 90 |
S+16 | 10 | 0 | 0 | 10 | 0 |
Date prévue | Stock avant | Besoin | Ressource | Stock après | Proposition |
---|---|---|---|---|---|
S | 12 | 100 | 200 | 112 | 0 |
S+1 | 112 | 0 | 0 | 112 | 0 |
S+2 | 112 | 0 | 0 | 112 | 0 |
S+3 | 112 | 0 | 0 | 112 | 0 |
S+4 | 112 | 0 | 0 | 112 | 0 |
S+5 | 112 | 0 | 0 | 112 | 0 |
S+6 | 112 | 0 | 0 | 112 | 0 |
S+7 | 112 | 0 | 0 | 112 | 0 |
S+8 | 112 | 0 | 0 | 112 | 0 |
S+9 | 112 | 0 | 0 | 112 | 0 |
S+10 | 112 | 0 | 0 | 112 | 0 |
S+11 | 112 | 0 | 0 | 112 | 0 |
S+12 | 112 | 0 | 0 | 112 | 0 |
S+13 | 112 | 100 | 0 | 12 | 0 |
S+14 | 12 | 0 | 0 | 12 | 0 |
S+15 | 12 | 100 | 0 | -88 | 200 |
S+16 | 112 | 0 | 0 | 112 | 0 |
Date prévue | Stock avant | Besoin | Ressource | Stock après | Proposition |
---|---|---|---|---|---|
S | 256 | 0 | 0 | 256 | 0 |
S+1 | 256 | 0 | 0 | 256 | 0 |
S+2 | 256 | 0 | 0 | 256 | 0 |
S+3 | 256 | 0 | 0 | 256 | 0 |
S+4 | 256 | 0 | 0 | 256 | 0 |
S+5 | 256 | 0 | 0 | 256 | 0 |
S+6 | 256 | 0 | 0 | 256 | 0 |
S+7 | 256 | 0 | 0 | 256 | 0 |
S+8 | 256 | 0 | 0 | 256 | 0 |
S+9 | 256 | 0 | 0 | 256 | 0 |
S+10 | 256 | 0 | 0 | 256 | 0 |
S+11 | 256 | 0 | 0 | 256 | 0 |
S+12 | 256 | 900 | 0 | -644 | 3000 |
S+13 | 2356 | 0 | 0 | 2356 | 0 |
S+14 | 2356 | 900 | 0 | 1456 | 0 |
S+15 | 1456 | 0 | 0 | 1456 | 0 |
S+16 | 1456 | 0 | 0 | 1456 | 0 |
- L'influence du stock de sécurité
- La gestion des composants communs
- Le cas des composants soumis à des besoins externes et des besoins internes
Date | S+3 | S+5 | S+16 | S+19 |
---|---|---|---|---|
Quantité | 12 | 40 | 90 | 50 |
Date | S+6 | S+10 | S+12 | S+15 |
---|---|---|---|---|
Quantité | 10 | 20 | 10 | 10 |
Date prévue | Stock avant | Besoin | Ressource | Stock après | Proposition |
---|---|---|---|---|---|
S | 53 | 0 | 0 | 53 | 0 |
S+1 | 53 | 0 | 0 | 53 | 0 |
S+2 | 53 | 0 | 0 | 53 | 0 |
S+3 | 53 | 12 | 0 | 41 | 100 |
S+4 | 141 | 0 | 0 | 141 | 0 |
S+5 | 141 | 40 | 0 | 101 | 0 |
S+6 | 101 | 0 | 0 | 101 | 0 |
S+7 | 101 | 0 | 0 | 101 | 0 |
S+8 | 101 | 0 | 0 | 101 | 0 |
S+9 | 101 | 0 | 0 | 101 | 0 |
S+10 | 101 | 0 | 0 | 101 | 0 |
S+11 | 101 | 0 | 0 | 101 | 0 |
S+12 | 101 | 0 | 0 | 101 | 0 |
S+13 | 101 | 0 | 0 | 101 | 0 |
S+14 | 101 | 0 | 0 | 101 | 0 |
S+15 | 101 | 0 | 0 | 101 | 0 |
S+16 | 101 | 0 | 90 | 11 | 100 |
S+17 | 111 | 0 | 0 | 111 | 0 |
S+18 | 111 | 0 | 0 | 111 | 0 |
S+19 | 111 | 0 | 50 | 61 | 0 |
S+20 | 60 | 0 | 0 | 61 | 0 |
Les propositions sur B deviennent des besoins induits pour EB et AB avec un décalage de 3 semaines (le délai de fabrication de B)
Date prévue | Stock avant | Besoin | Ressource | Stock après | Proposition |
---|---|---|---|---|---|
S | 0 | 100 | 120 | 20 | 0 |
S+1 | 20 | 0 | 0 | 20 | 0 |
S+2 | 20 | 0 | 0 | 20 | 0 |
S+3 | 20 | 0 | 0 | 20 | 0 |
S+4 | 20 | 0 | 0 | 20 | 0 |
S+5 | 20 | 0 | 0 | 20 | 0 |
S+6 | 20 | 0 | 0 | 20 | 0 |
S+7 | 20 | 0 | 0 | 20 | 0 |
S+8 | 20 | 0 | 0 | 20 | 0 |
S+9 | 20 | 0 | 0 | 20 | 0 |
S+10 | 20 | 0 | 0 | 20 | 0 |
S+11 | 20 | 0 | 0 | 20 | 0 |
S+12 | 20 | 0 | 0 | 20 | 0 |
S+13 | 20 | 100 | 0 | -80 | 90 |
S+14 | 10 | 0 | 0 | 10 | 0 |
Date prévue | Stock avant | Besoin | Ressource | Stock après | Proposition |
---|---|---|---|---|---|
S | 125 | 100 | 0 | 25 | 0 |
S+1 | 25 | 0 | 0 | 25 | 0 |
S+2 | 25 | 0 | 0 | 25 | 0 |
S+3 | 25 | 0 | 0 | 25 | 0 |
S+4 | 25 | 0 | 0 | 25 | 0 |
S+5 | 25 | 0 | 0 | 25 | 0 |
S+6 | 25 | 10 | 0 | 15 | 0 |
S+7 | 15 | 0 | 0 | 15 | 0 |
S+8 | 15 | 0 | 0 | 15 | 0 |
S+9 | 15 | 0 | 0 | 15 | 0 |
S+10 | 15 | 20 | 0 | -5 | 200 |
S+11 | 195 | 0 | 0 | 195 | 0 |
S+12 | 195 | 10 | 0 | 185 | 0 |
S+13 | 185 | 100 | 0 | 85 | 0 |
S+14 | 85 | 0 | 0 | 85 | 0 |
S+15 | 85 | 10 | 0 | 75 | 0 |
S+16 | 75 | 0 | 0 | 75 | 0 |
Pour la matière première MP, les besoins sont des besoins induits par la fabrication de EA et EB.
En J+12, il existe un besoin B de
B = 12*90 + 10*90 = 1980
Date prévue | Stock avant | Besoin | Ressource | Stock après | Proposition |
---|---|---|---|---|---|
S | V | 0 | 0 | 256 | 0 |
S+1 | 256 | 0 | 0 | 256 | 0 |
S+2 | 256 | 0 | 0 | 256 | 0 |
S+3 | 256 | 0 | 0 | 256 | 0 |
S+4 | 256 | 0 | 0 | 256 | 0 |
S+5 | 256 | 0 | 0 | 256 | 0 |
S+6 | 256 | 0 | 0 | 256 | 0 |
S+7 | 256 | 0 | 0 | 256 | 0 |
S+8 | 256 | 0 | 0 | 256 | 0 |
S+9 | 256 | 0 | 0 | 256 | 0 |
S+10 | 256 | 0 | 0 | 256 | 0 |
S+11 | 256 | 0 | 0 | 256 | 0 |
S+12 | 256 | 1980 | 0 | -1724 | 3000 |
S+13 | 1276 | 0 | 0 | 1276 | 0 |
S+14 | 1276 | 900 | 0 | 376 | 0 |
S+15 | 376 | 0 | 0 | 376 | 0 |
Date prévue | Stock avant | Besoin | Ressource | Stock après | Proposition |
---|---|---|---|---|---|
S | 256 | 0 | 0 | 256 | 0 |
S+1 | 256 | 0 | 0 | 256 | 0 |
S+2 | 256 | 0 | 0 | 256 | 0 |
S+3 | 256 | 0 | 0 | 256 | 0 |
S+4 | 256 | 0 | 0 | 256 | 0 |
S+5 | 256 | 0 | 0 | 256 | 0 |
S+6 | 256 | 0 | 0 | 256 | 0 |
S+7 | 256 | 0 | 0 | 256 | 0 |
S+8 | 256 | 0 | 0 | 256 | 0 |
S+9 | 256 | 0 | 0 | 256 | 0 |
S+10 | 256 | 0 | 0 | 256 | 0 |
S+11 | 256 | 0 | 0 | 256 | 0 |
S+12 | 256 | 1980 | 0 | -1724 | 3000 |
S+13 | 1276 | 0 | 3000 | 4276 | 0 |
S+14 | 4276 | 900 | 0 | 3376 | 0 |
S+15 | 3376 | 0 | 0 | 3376 | 0 |